Material Efficiency and 3R Objectives
|
Abstract:
Material efficiency is a foundational element in achieving 3R (Reduce, Reuse, Recycle) objectives, aiming to use fewer resources, generate less waste, and enhance overall productivity. This concept applies across various sectors, notably in building construction and manufacturing, by integrating strategies such as Design for Environment, Life-cycle Assessment, and resource-efficient design and production.
Each stage of a building's or product's lifecycle (from design and specification to use and end-of-life) offers opportunities to apply material efficiency principles. These include minimizing raw material use, enhancing energy and water efficiency, and facilitating reuse and recycling. By adopting a whole-system approach, material efficiency not only contributes to environmental sustainability but also leads to cost savings and improved performance across the value chain.
Keywords:
material efficiency, 3R policy, lifecycle assessment, green buildings, sustainable manufacturing, design for environment, resource efficiency, waste reduction
|
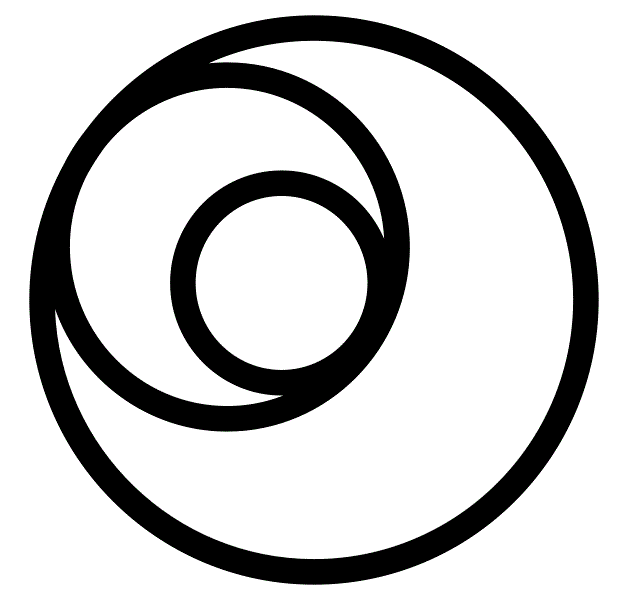 |
Hari Srinivas |
Concept Note Series E-098. June 2015.
|
M aterial efficiency concerns the use of materials or physical processes that uses less material, produces higher outputs/outcomes, and generates less wastes. It is a key pillar in achieving the objectives of a 3R policy.
Material efficiency strategies include, for example, products that last longer, remanufacturing and modular manufacturing, reuse and recycling of product components, using less material in product designs, or redesigning manufacturing processes to use less energy, less water or less raw materials. It can also include replacement of scarce and expensive elements, notably those critical for energy applications.
Greater material efficiency can be achieved through strategies such as Design for Environment, Life-cycle Assessment, Energy and Water Efficiency etc. In fact, material efficiency and energy efficiency go together, and help not only in reducing manufacturing costs, but also in reducing emissions and wastes (and associated costs).
Best results in material efficiency are achieved by influencing early on through planning and promoting Design for Environment. In an optimal situation the whole value chain will benefit from life cycle considerations in product development.
Humans spend more that 60-80 percent of their time within a building or in a built environment. This is where the potential of material efficiency can be fully realized as architectural design and building construction. In all stags of a building - from design and specification, to construction and use, and to the final decommissioning and disposal, the concept of material efficiency can be fully tested.
Aiming for a "Green Building", an analysis of a building will usually cover all stages of its lifecycle:
Lifecycle stage |
Tools, Strategies and Typical actions |
Architectural design |
Using the concept of "Design for Environment" where all aspects of a building's impacts on the local environment are considered, right at the design stage itself. Along with material efficiency, energy and water efficiency aspects are also considered. Both passive design elements, and active elements are used to achieve better efficiency. |
Building specifications |
A huge range of materials - both raw as well as assembled - go into the construction of a building or structure. This stage of a building provides a number of opportunities to aim for material efficiency, including, for example - the reduced use of scarce materials, materials that create comfortable indoor environments (reducing the need for energy to heat or cool a building), use of recycled rather than raw materials (especially for wood products), etc. Using appropriate building codes and ISO standards, such as ISO 50001 for energy efficiency will also help in this stage. |
Construction |
Aiming for better material efficiency also provides a number of opportunities during the construction phase of a building's lifecycle. This is particularly true in terms of ensuring that materials are not unduly wasted, or less water and energy is used in the processes. Modularization and component systems also help in reducing material use and increase their efficiency. |
Use |
This is where, in the day-t-day use of a building that maximum efficiency can be achieved, particularly in energy efficiency. While the previous stages will reduce the dependence on energy for heating, cooling, or overall aspects of a building, it is at this stage of a building life-cycle that most of the 'problems' or efficiency arises (and where most of the solutions can also be implemented!). Using appropriate building codes and ISO standards, such as ISO 14001 for environmental management systems will also help in this stage. |
Decommissioning and disposal |
This stage has not been well researched or explored in terms of material efficiency, but essentially looks at the way in which the design, specification construction and use of a building can be carried out so that its various components and materials can easily be reused, recycled or otherwise properly disposed with a minimum impact on the environment. |
A similar analysis for material efficiency in a factory can also be made, looking at the entire life-cycle of a product or service. In fact, material efficency is a well established concept in designing manufacturing blueprints. For example, a typical strategy to increase material efficiency will cover a systematic evaluation of material flows in production (material balance of factory and processes) or tracing direct and indirect costs related to material use.
- For example, in the design stage, the 'usual' objectives of user preferences and marketability, can be sumplemented by material efficiency ones of using materials with less environmental impact or using less meterial in itself.
- In the manufacturing stage, efforts can be made to use fewer resources (material, energy, water etc.) or produce less pollution and waste. The concept of material efficiency can also be extended to reducing the impact of distribution and sales.
- In the use stage, again material efficiency approach has a key role to play in using fewer resources, causing less pollution and waste, and optimizing functionality and service life.
- Much attention has recently being paid to the end-of-life or a product or service. Issues such as reducing the environmental impact of disposal, making reuse and recycling easier are considered at this stage.
It also includes identification of locations where improvement can be made, and concrete actions to achieve these improvements. Estimate of benefits, feasibility and savings of the suggested actions as well as possible recommendations for further assessment are also made, along with consideration of environmental aspects of production and materials.
|